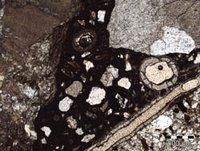
Betonfahrbandecke.

eines geschädigten Betons.
Riss und Luftpore im rechten Bildabschnitt
sind mit Alkali-Silica-Gel gesäumt.
Among the key activities of the Chair of Ceramics is research in the field of alkali-aggregate reaction. Alkali-aggregate reaction is a bursting reaction caused by certain reactive aggregates. Under unfavourable conditions AAR may lead to a total disintegration of a concrete structure. Harmful aggregates always contain reactive silica (SiO2) which is characterized by a high disorder in the crystal lattice. Dependent on the degree of disorder amorphous, crypto- to microcrystalline and stressed silica – with contortions of the SiO2 network due to tectonic loads – can be distinguished. Reactivity thereby is a function of disorder. There are rapid reacting aggregates (e.g. opal sandstone and flint) and slow/late reacting aggregate (e.g. stressed quartz).
Damages may occur after 2 – 5 years for rapid reacting aggregates, but may also take up to 10-15 or more years for slow/late reacting aggregates to appear. Besides reactive aggregates a high humidity in the concrete and sufficient levels of alkalis are necessary for AAR to take place.AAR constitutes a huge problem in numerous countries around the world – among them e.g. Canada, Denmark, Iceland, China and also Germany. In these countries AAR has therefore become topic of many research works. In Austria AAR has rather been in the background – up until 2003 only two damage cases have been reported of.
Aim of the work at the Chair of Ceramics is the built-up of know-how in Austria. Thereby an emphasis is put upon the identification and assessment of Austrian AAR damage cases. International accepted diagnose methods are evaluated for their applicability and adapted to Austrian needs if necessary. Damage rating indices which allow the quantification of damage with simple petrographic methods are of special interest.
Ziel der Arbeiten am Lehrstuhl für Gesteinshüttenkunde ist ein Know-How-Aufbau hinsichtlich der Alkali-Gesteinskörnungsreaktion in Österreich. Ein Schwerpunkt ist dabei die Identifikation und Beurteilung der AGR an österreichischen Schadensfällen. Dabei werden international anerkannte Diagnosemethoden auf deren Eignung geprüft und gegebenenfalls adaptiert. Besonderes Interesse gilt sogenannten Schadenskennzahlen, die eine Quantifizierung des Schadens mit einfachen petrografischen Untersuchungen ermöglichen.
Another emphasis is the testing of damaged concretes with non-destructive testing techniques. With in the laboratory produced and damaged concretes the effect of AAR on the mechanical properties of the concrete is investigated.
References:
Harmuth, H., Fischböck, E.: Identifikation und Beurteilung der Alkali-Zuschlag-Reaktion. Bundesministerium für Verkehr, Innovation und Technologie, Straßenforschung Heft 560, 2006.
Fischboeck, E.K., Harmuth, H.: An Austrian experience with identification and assessment of alkali-aggregate reaction in motorways. Proc. of the 2 nd International Conference of Concrete Repair, Rehabilitation and Retrofitting. Cape Town, Südafrika, November 2008.
Computer simulations are applied for investigations of complex systems for which simple closed form analytic solutions are not possible. To gain insight into the operation of those systems a simplified model is required. Numerical methods enable the prediction of the behaviour of the model from a set of parameters and initial conditions. Based on results of the computer simulations conclusions for the real system can be drawn.
A main effort of the chair of ceramics is to clarify wear mechanisms of refractories. Refractories are used to prevent the steel shell of furnaces and aggregates form high temperatures. In high-temperature processes melts and slags occur. In addition to the thermo-mechanical load the refractory has to withstand the chemical attack of these liquid substances. Thereby the concurrent wear mechanisms are affected by the fluid dynamics of the melts and slags within the aggregate. To investigate this influence of the fluid flow CFD-simulations (computational fluid dynamics) are applied for example in the case of the laboratory rotary kiln that is used to determine the slagging resistance of refractories.
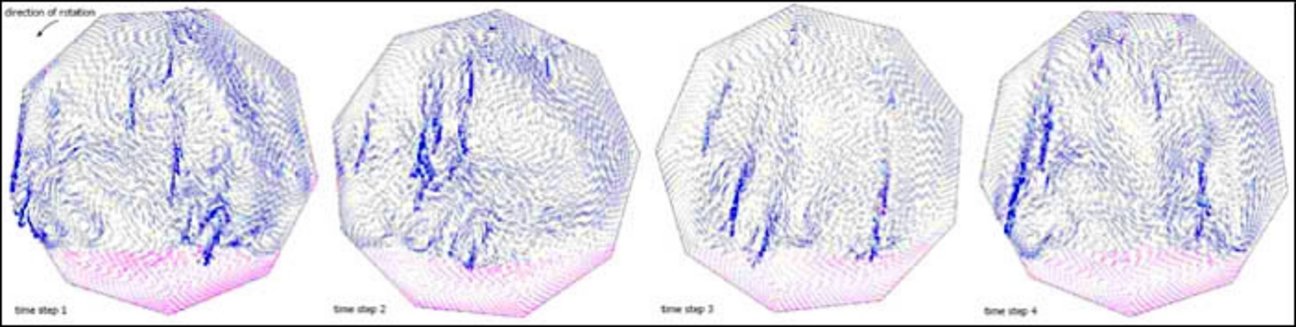
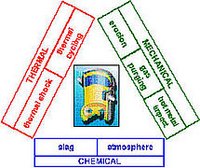
Refractories are materials used to line commercial furnaces such as steelmaking vessels, glass tanks and cement kilns. Refractories in metallurgical vessels must resist high temperatures (up to 1650 °C) but also mechanical stresses (erosion, abrasion) and the attack by corrosive atmospheres and liquids (molten metals, slags). The attack of refractories is a complex phenomenon, as the corrosion mechanisms act synergistically.
The research group “Melt corrosion of refractories in metallurgical vessels” deals with the description of the chemical wear. The melt corrosion occurs in two steps for porous, ceramically bonded materials: penetration of the slag into the refractory via open pores and dissolution of the refractory components into the slag. The ion flux j caused by the dissolution process is governed by Fick’s First Law:
According to the equation above, the corrosion rate is a function of many variables including characteristics of the refractory and the slag as well as predominant process conditions. Thus, to reduce the wear rate of refractories in metallurgical vessels emphasis must be placed on the one hand on product development but on the other hand on the steelmaking practice with regard to slag chemistry and service conditions. The investigations presented here comprise the characterisation of different metallurgical slags (eg ladle, converter, EAF) as the attacking medium and the description of different refractory/slag equilibria.
The objectives of the research area are
- Description of the main corrosion mechanisms in different metallurgical vessels
- Establishment and evaluation of new corrosion models
- Identification of possibilities to reduce the wear-rate: process performance, lining design, product selection, product development
Approach/Methodology
The investigations focus on the characterisation of slags and refractory/slag equilibria using thermochemical (FactSage), mineralogical (XRD, SEM, EDX) and analytical tools.
Characterisation of metallurgical slags
- Phase constitution in dependence of temperature and atmosphere
- Melting behaviour (solidus and liquidus temperature, amount of liquid)
- Physical properties of the slag (eg viscosity, diffusion coefficient)
Characterisation of refractory slag/equilibria
- Identification of corrosion environments (eg slag chemistry, temperature)
- Post-mortem investigations of industrial refractories and laboratory scale corrosion tests (cup test, rotary slag test, induction furnace test)
- Description of the dissolution behaviour of refractories in slags in dependence of process conditions (eg phases formed at the interface, solubility limit)
Reference
F. Melcher, V. Reiter, H. Harmuth: Investigation of refractory/slag equilibria in steel ladles. Präsentiert bei: Calphad XXXVI, Pennsylvania State University, 2007.
Contact : Franz Melcher, Viktoria Reiter
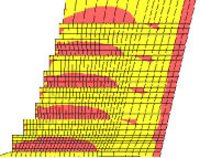
The cost-effective application of building materials is of growing importance, thus measures for optimisations are still of special interest. Computational methods were used to predict the behaviour under their respective boundary conditions. The simulation of the thermo-mechanical behaviour of refractories represents a research area at the chair of ceramics.
Refractories were mainly used in industrial vessels to protect the steel construction from high process temperatures. Theses vessels are widespread, for example in metallurgical industry, glass industry, chemical as well as in the building materials industry. Based on their application, refractory materials reach temperatures of more than 1500°C. Mechanical stresses appear in the lining due to the thermal expansion and the mechanical constraints. These loads facilitate mechanical failure and can accelerate the wear rate of the refractory material and necessitate a premature replacement of the refractory product.
The behaviour of the lining can be improved with adequate selection of the materials, optimisation of geometry or adaptation of process parameters. For this purpose simulations using Finite Element Methods (FEM) are carried out at the chair of ceramics. To clarify failure mechanisms it is necessary to allow for nonlinear material behaviour especially in the course of crack formation.
With this numerical tool it is possible to analyse for example the loads in the bottom/wall transition zone of a LD-converter in which carbon-rich hot metal is converted into steel.
The thermal expansion of the lining in the bottom and the wall induces a bending moment in the bricks of the transition zone. At the right side of the figure the stresses in radial direction are shown in a contour plot. Zones with tensile stresses are red and zones with compressive loads are coloured yellow. These bending stresses lead to crack formation parallel to the hot face, which can cause spalling of brick parts.
References
D. Gruber, K. Andreev, H. Harmuth: Optimisation of the Lining Design of a BOF Converter by Finite Element Simulations. Steel Research int. 75 (7), 455-461, 2004
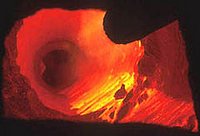
Prediction of the chemical loading of refractories in cement rotary kilns by means of process simulation
A variety of influences contributes to wear of refractories in cement rotary kilns and cause a chemical, mechanical and thermal loading of the lining. See: Melt corrosion of refractories in metallurgical vessels. Only the chemical aspect and its impact on the brick lining of the rotary kiln itself shall be considered here, especially the action of alkali salts (sulphates, chlorides).
A decisive parameter for refractory wear is the degree of sulfatisation DS which may be expressed as the molar ratio of sulfate and chlorine to alkalies:
The following wear mechanisms may occur in dependence of the DS:
- For a DS > 1 a sulfate corrosion of the lime content of the binder phase of basic refractories – especially dicalcium silicate (C2S) – may be expected.
- For a DS < 1 e.g. the formation of alkali chromate sulfates may take place in the case of magnesia chromite refractories and thus lead to wear of the chromite component.
- In the case of DS = 1 salt infiltration is expected to behave chemically inert, but salt melts migrate into the bricks and fill up the pores until they solidify. When the lining is cooled in the case of a shutdown the infiltrated part of the brick behaves more brittle and spalling may occur especially at the border between infiltrated and non-infiltrated part.
Alkali salts are mainly accumulated by an evaporation/condensation process interacting between the kiln atmosphere and the kiln feed, and are infiltrated into the bricks by condensation from the vapour phase. The considerations quoted above show the importance to control this process and to know about its influence on the amount of alkalies and the composition of alkali salts condensed.
In many cases it is desirable to predict the loading of refractories by alkali salts in dependence of varying process parameters. Especially changes of fuel are of great importance nowadays. Introduction of petrol coke may significantly rise the sulfur input; polymers may contain chlorine. A prediction of the volatile recirculation caused by a change of the fuel may e.g. help to optimise refractory selection and estimate the impact of process technology on wear.
In order to fulfill this goal calculation of volatile recirculation is performed by means of process simulation using commercial software packages FactSage™, SimuSage™ and Borland Delphi™. For simulation purposes reactors are defined to model all elementary process steps, e.g. the preheater stages and the calciner. The rotary kiln itself is discretised into several sections, each of them represented by a reactor. These reactors establish balances governing mass and heat transfer, and enable the calculation of chemical equilibrium. The total of these balances sets up a nonlinear system of simultaneous equations which is solved by a numerical iteration procedure. As a result, the chemical composition of all solid and gaseous mass fluxes is available. In combination with a thermal simulation of the kiln lining the infiltration of alkali salts into the refractory can be calculated additionally.
A further goal is an easy to handle user interface in order to facilitate the applicability of the process simulation for different cement plants.
References
Emler, R.; Harmuth, H.; Nievoll, J.: Prediction of the chemical loading of refractories in a cement rotary kiln by means of process simulation. - in: UNITECR '07 - Unified International Technical Conference on Refractories. (2007), S. 577 – 580.
Emler, R.; Harmuth, H.: Prediction of the chemical loading of refractories in cement rotary kilns by means of process simulation. - in: 9th Annual GTT-Technologies Workshop. (2007).
![Abb. 1 (oben): Heiztischmikroskopische Untersuchung<br>der Kristallisation einer Gießschlacke.<br> Die Pfeile kennzeichnen die Cuspidinkristalle [2] csm_Giesspulver_Koelbl_6f0ab5d907](/fileadmin/_processed_/2/8/csm_csm_Giesspulver_Koelbl_6f0ab5d907_23192b774a.jpg)
der Kristallisation einer Gießschlacke.
Die Pfeile kennzeichnen die Cuspidinkristalle [2]
One of the main research interests of the chair of ceramics is the investigation of the structure of mould powders and slags as well as the characterisation of their melting and solidification behaviour. For these purposes original mould powders and samples taken from service (mould slags, slag rims) are analysed.
The therefore applied methods are listed below:
- Reflected light and scanning electron microscope for mould powder, mould slags and samples annealed at selected temperatures (fig. 1 and fig. 2)
- Hot stage microscope (fig. 3 and fig. 4) for investigation of mould powders, polished sections of mould powder specimen, as well as mould slags at temperatures up to 1500°C
- XRD
- Differential thermal analysis and thermogravimetry
- Investigations using the double hot thermocouple technique (DHTT) (fig. 5): There the crystallisation behaviour of a mould slag in dependence of the temperature gradient is observed.
- High temperature viscometer (fig. 6)
The characterisation of mould powders using the methods quoted above makes it possible to draw conclusions concerning operating performance and mould powder selection.
References
[1] I. Marschall, H. Harmuth: “Investigation of the slag rim growth in the continuous casting process”, SCANMET III- 3rd International Conference on Process Development in Iron and Steelmaking, 8-11 June 2008, Luleå, Sweden
[2] N. Kölbl, H. Harmuth: „Hot stage microscopy for in situ observations of the melting and crystallisation behaviour of mould powders”, SCANMET III- 3rd International Conference on Process Development in Iron and Steelmaking, 8-11 June 2008, Luleå, Sweden
Contact: Nathalie Kölbl, Irmtraud Marschall